Increase profitability & reduce business risk by collaborative B2B plastics reuse & recycling
The Triple Bottom Line Revisited
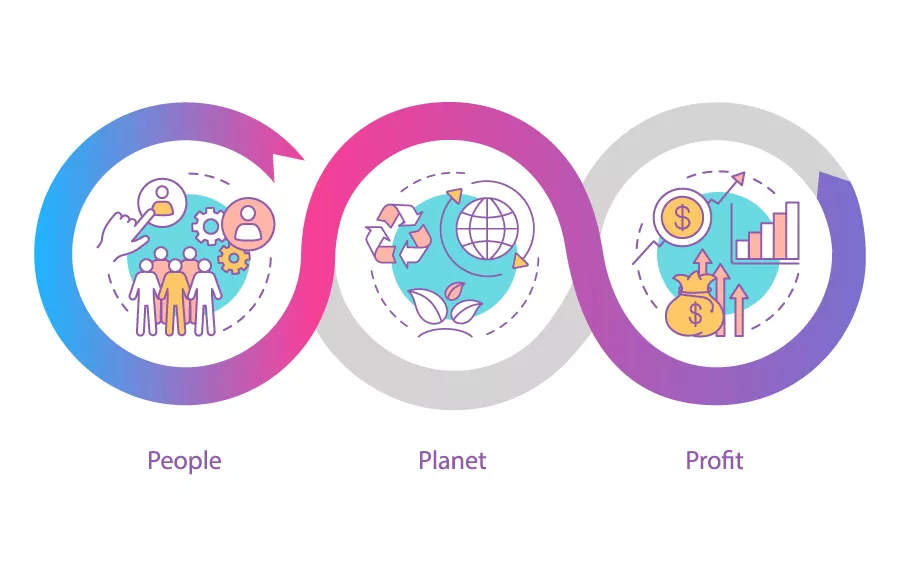
John Elkington coined the phrase ‘Triple Bottom Line’ in 1994 to propose a model for sustainable business that balanced economic, social and environmental impacts and outputs. Looking back at it 25 years later, he could see that there was still a long way to go for most companies, but some very successful companies were benefiting from applying this approach.
Table of Contents
Today more than ever before, the gathering pace of climate change, resource shortages, the Covid-19 pandemic, and international conflicts are all reducing market and business stability and generating a range of social actions and legislative measures focused on environmental protection.
As a manufacturer of plastic fasteners, NIFCO needs to maintain constancy and quality of supply to deliver high quality products, and to do this in a sustainable way. Our philosophy is to deliver the ‘best fit’ solution for people and planet, and this underpins our approach to all aspects of our business.
This sounds great, but it’s actually a lot of work to build a genuinely triple bottom line business, especially when you need to manage plastics reuse and recycling logistics. So let’s have a look at what’s required, what has contributed to Nifco’s success, and some ideas for making even bigger gains for your triple bottom line.
Accepting The Challenges Of Plastics Reuse & Recycling
Why do companies use a lot of new plastic in their products when most plastics can be easily recycled? From the point of view of consumers it seems reckless and irresponsible for companies to continue to order in fresh plastics to continue to manufacture tonnes of new products when there is already so much plastic waste clogging up the environment.
The reality is that reusing and recycling plastics usually ends up in the ‘too hard’ box for most manufacturers – and by ‘too hard’ we really mean ‘too expensive.’ We know consumers who vote with their environmental conscience when making choices between products, but in these troubled economic times consumers also make choices based on price alone.
Switching to reuse and recycling is seen as a risky step to take by many businesses, but it isn’t as risky as you might think. Reuse is low risk because you know the plastic you are reusing is fit for purpose, and it’s obvious that if you can reuse your in-house waste in new products you are saving on material costs, waste storage and management. A win-win-win situation…
ReNifco: An Effective In-House Plastic Reuse System
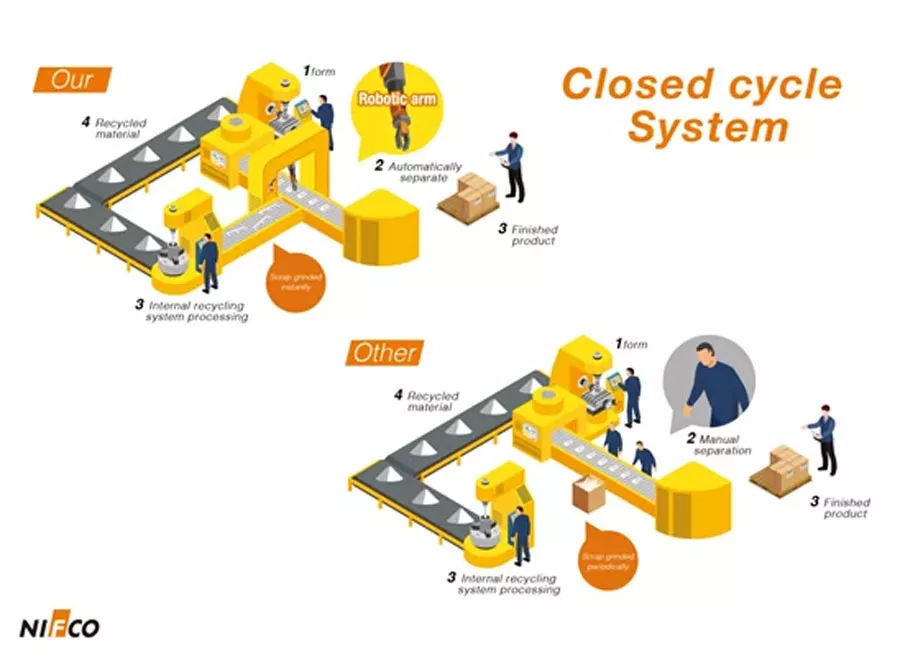
At Nifco we have an in-house production line waste reclaim and reuse system that does exactly this, we call it ‘ReNifco’ and it effectively eliminates waste plastic from our production runs. Most companies that manufacture plastic products, especially injection molding in POM, ABS and other easily managed thermoplastics, can reuse their production line offcuts, sprues and waste.
In-house reuse makes perfect sense for almost every manufacturer of plastic products, but using recycled materials brings challenges. Most of these come from the fact that you are buying a commodity that is supposed to be the same as the ‘new’ material, but you can’t always be entirely sure of its quality.
Solving The Recycled Plastic Problem
The problem with recycled plastics for manufacturers of high quality products is the need for raw materials that are clean and uncontaminated by other plastics, or metal chips, springs and clips that can make their way into the recycled product, but are bad news for injection molding machines.
Ideally, if you were going to order recycled plastic from a supplier you would want to be absolutely sure of the quality and consistency of what you were getting. This is why reputable plastics recyclers conform to ISO standards and can provide paperwork to demonstrate the source and characteristics of plastics they offer.
In the perfect world, you would have the same confidence in recycled plastics that you have about the new plastics you reuse in your own manufacturing process. Fortunately there is a way to do this. You can achieve this goal through direct B2B collaboration with other manufacturers of plastic products.
The B2B Plastics Reuse Supply Chain
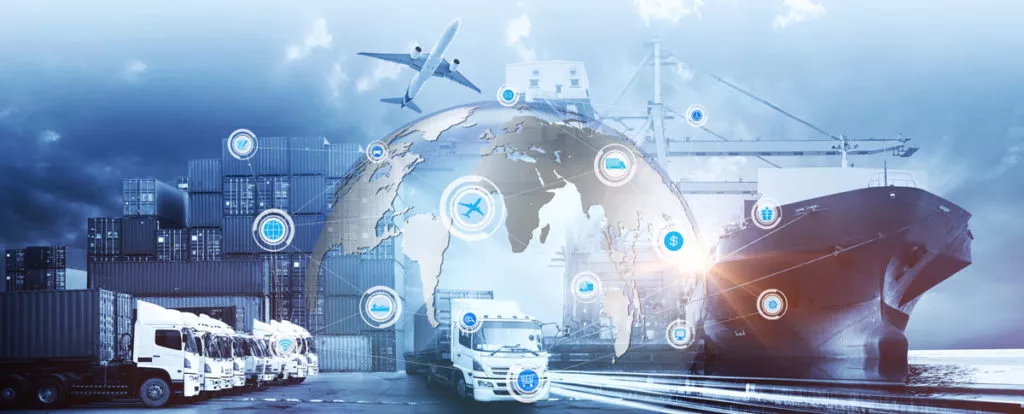
Let’s imagine you are a company making plastic fasteners, and you need a consistent supply of high quality POM plastic to do this. There are three possible supply chain routes to obtain the POM you need:
- New POM
- Recycled POM
- Waste POM From Production
You want to minimize your use of new POM because that’s bad for the environment, and you’re not sure about the quality or reliability of supply for recycled POM. You already use your own waste POM from your production line, and you don’t have enough of that… but what about the waste POM that other manufacturers are producing?
Reusing B2B Waste From Trusted Partners
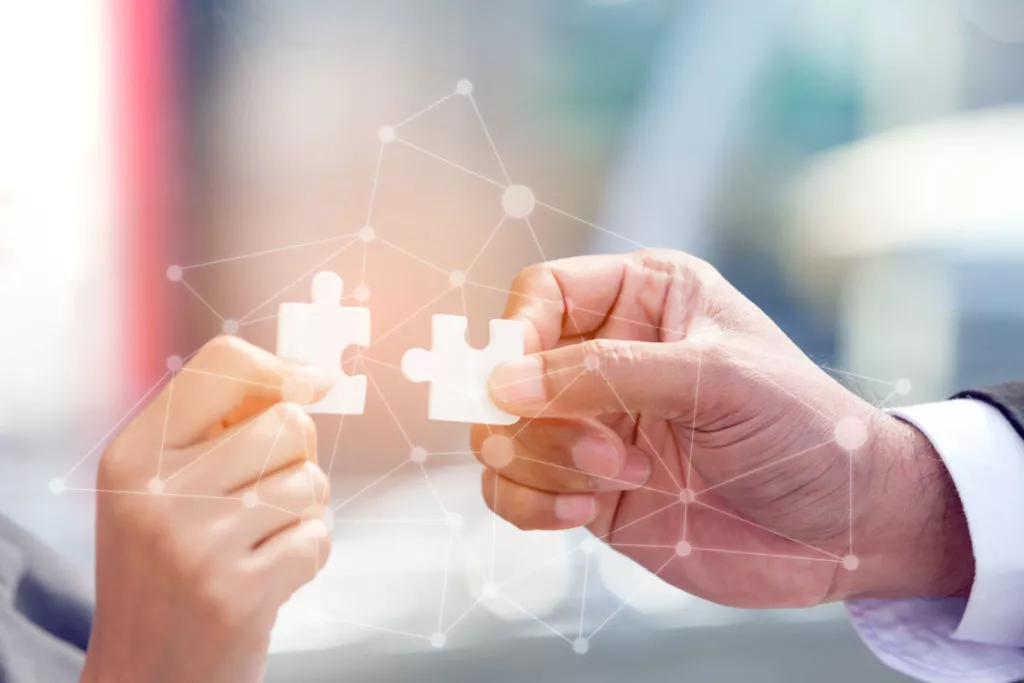
There are two potential types of business partner that might be able to provide you with B2B plastic waste that you can reuse with confidence. The first are your existing business customers and the second are businesses who manufacture products from the same types of plastics that you do. The icing on the cake is if they also use the same colors…
Offering to reuse plastics from your own customers is a win-win proposal that offers potential cost-savings, reduces environmental impacts (remember the triple bottom line…) and adds resilience to your existing business relationships. At Nifco we are already working closely with our customers to maximize our mutual benefits from collaborative recycling ventures.
The other option is to approach companies that you are sure will have waste plastic of a quality you can use, and which, ideally, you can reprocess in your own in-house production reuse system – which you need to set up now if you haven’t already got one. This is the key to doing in-house recycling of plastics from other sources. But where do you go to find these companies?
Looking Closer To Home
The stress of maintaining consistency of supply in the logistically stretched times of the Covid-19 pandemic have led many companies to look closer to home for their materials. This applies to looking for potential business partners who might be able to supply reusable plastic waste.
Modern high-density business parks and industrial centers found in Taiwan, mainland China, Vietnam and other Southeast Asian countries are good places to be based if you are looking for possible supply chain sources of plastics for reuse. The close proximity of companies manufacturing a range of products of different qualities makes it more likely that you will discover a business partner who uses plastics of equal or higher quality to the ones you require.
The Benefits of Local Collaboration to Reuse Plastic Waste
- Savings on transportation, warehousing and logistics costs
- Safeguarding raw materials supplies
- Reducing unavoidable waste
- Maximizing recycling and reuse of lightweight and hard to transport waste
There are so many benefits of collaborating with other businesses to reuse plastic waste that it’s hard to pick just a few to focus on. The major benefits come from increasing the local availability of raw materials that you need and reducing the costs of storage, transportation and disposal of waste. Since most plastic waste is very light, transport costs per tonne can be surprisingly high.
Having access to sources of raw materials close to your manufacturing base is a major benefit in safeguarding supply and also reducing the cost of raw material transport to your site. For Nifco it’s a case of think local, export global.
The Circular Economy: Manufacturing Tiers & Reuse
Nifco is a major producer of plastic fasteners and components for the automotive industry. Due to regulatory constraints and requirements for material standards, most automotive manufacturing uses new plastics of very high quality. This means that any manufacturing plastic waste generated is going to be of a suitable quality for reuse in almost any other product.
We can classify plastics manufacturers into three ‘tiers’ of quality – tier one manufacturers, like automotive, medical, and some food packaging companies, require very consistent, high quality new plastics for their products. They also may be limited in their capacity to reuse plastics in their own production lines because of the risk of contamination or lack of space.
Tier two manufacturers do not need to use new plastics, but do need to use high quality materials with reliable characteristics to meet designed engineering requirements. This applies to a wide range of businesses, including the buckle and fastener division of Nifco.
Tier three manufacturers do not need to use high quality plastics, can readily use recycled plastics, and sometimes even contaminated or mixed plastics. Some companies with a wide range of products may manufacture goods in multiple tiers. Nifco works across all three tiers depending on the product type and sector. This enhances our reuse and recycling options.
So, if you are planning to reuse plastics from another manufacturer, the easiest way to ensure that their waste plastic will be fit for your purposes is to work with companies that are in a tier above your own. This means for our fastener and buckle products we can be pretty certain that we can reuse automotive plastic waste to manufacture new products without any problems.
Discover Nifco’s Best Fit Solutions For Plastic Reuse
At Nifco, we continuously innovate to find new solutions with industry partners to manage and improve our supply chain sustainability. We already regrind and reprocess in-house plastic waste, and produce designs that reduce material use without compromising quality and performance.
For a successful and sustainable industry it’s necessary to shift focus onto the supply chain logistics of recycling systems. It makes sense to look at integrated cross-corporation and cross-industry recycling. This is especially true in high density industrial parks. Picking compatible quality tier partners offers quality guarantees and peace of mind.
The Nifco philosophy is to solve customer challenges by discovering the best fit possible between design, function and appearance. Contact us to discover how our technological advances and design excellence meets the challenges arising from the need to protect and conserve our environment.